Red Tape, Remedial Cladding and Compliant Solutions
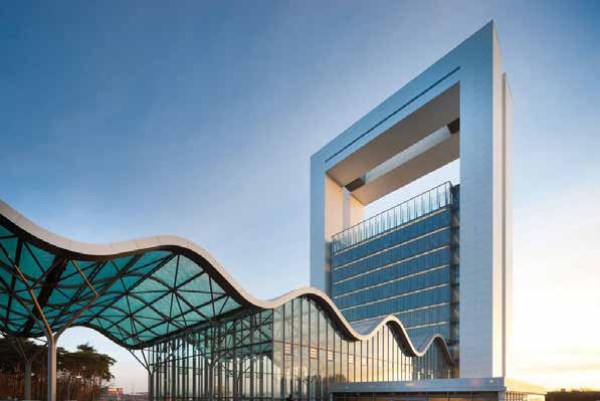
Due to significant changes to the BCA (Building Code of Australia) some insurers, specifiers and strata advisers might default to a total ‘no use of composites’ policy, in which they hope to find surety. But conflating simplicity with surety, isn’t recommended. Some specify “only solid steel panels”, hoping that’s a cure-all for façade remediation.
But such simplistic thinking ignores a whole new set of BCA compliance requirements (relating to condensation and damp mandatories, for example) that might just kick newer and more costly repair problems further down the road.
So how do responsible practitioners find enduring rectification solutions that have the credentials, documentation and test results that offer complete confidence?
The bad news is there is no single product or brand that remediates every ‘at risk’ façade issue. Compliance isn’t just about PE, it’s about system safety as the Shergold Weir Report confirms.
Discussions with your provider should inform you, for example, that because cladding compliance is more of a façade system issue than a product ‘varietal’ problem, there are multiple paths to securing compliance.
For easy reference, there are still three routes that provide compliance for external walls (EW):
1) Verification Method CV3; using a fullscale façade test to the peak Australian standard AS5113
2) Deemed to Satisfy; Deemed NonCombustible, via a combination of rigorous small-scale, laboratorybased performance testing
3) Performance Assessment; façadespecific evaluation by a fire engineer based on full scale tests Savvy certifiers, insurers and strata managers who really understand the ‘multiple paths to compliance’ reality are better placed to compliantly remediate façades, more costeffectively.
Fairview Architectural was the company chosen and trusted to provide the remediation cladding for Australia’s biggest façade fire. After fire engulfed ‘Lacrosse’ in Melbourne, an extensive screening process involving numerous parties from Melbourne City Council, Victorian Building Authority, Metropolitan Fire Brigade, plus independent fire engineers, building surveyors, and strata management, Fairview’s Vitracore G2 was chosen to replace non-compliant ‘PE panels’ and safely return Lacrosse to its former glory.
Similarly, when Sydney’s Northpoint Tower showed signs of pebblecrete corrosion and de-lamination, Fairview again supplied its DtS, deemed noncombustible Vitracore aluminium cladding panel to add safety, durability and a modern look to the $15million refurbishment.
The examples list of projects Fairview has helped remediate just go on and on… Shelley Street in Sydney saw Alucobond PE come off and Vitracore G2 go on; At Eden Drive in Macquarie Park, PE came off and G2 went on; In Coronation Drive in Milton QLD, and PE came off to be replaced by Vitradual.
If you are navigating your way through a re-cladding project due to use of non-compliant or ageing products, the Remedials Team at Fairview is dedicated to providing a start-to-finish solution for any and all options to help you replace dodgy cladding. A provider must have the knowledge or range that matches every compliance pathway, and the Fairview compliant rectification products include:
• Vitracore G2 – Australia’s leading, profiled aluminium structure core composite cladding Vitrashield – a solid steel panel with components often found in a lightweight commercial wall build
• Vitradual 3mm – a durable, impact resistant non-combustible solid aluminium cassette cladding
• Stryüm – intelligent aluminium façade available in a range of high-quality plate façade panels
• Equitone (NSW only) – a pre-finished, high density fibre cement façade panel
View Comments
(0)