Early Planning the Key to Remediating Flammable Cladding
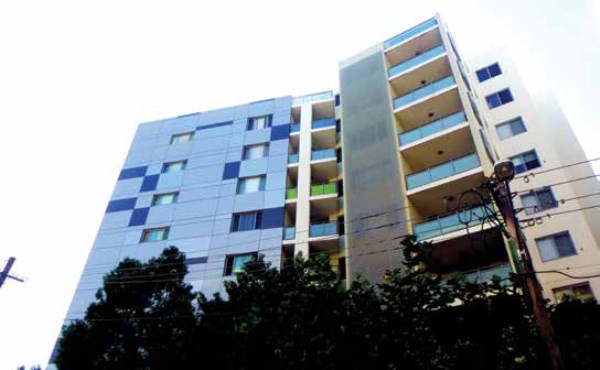
Q&A
An interview with Paynter Dixon Business Development Manager, Marija Petrovska
The fall-out from the 2017 Grenfell Tower fire in London continues to reverberate throughout the international building industry.
The investigation into the fire that killed 70 people shone a light on the popular but potentially deadly aluminium cladding products used extensively on buildings around the world, including here in Australia.
In New South Wales, hundreds of buildings are clad in the aluminium composite material, and many don’t meet the current building codes.
For building owners, it is a complex and potentially costly problem which can require the replacement of an entire building’s exterior.
Paynter Dixon Business Development Manager, Marija Petrovska, says there is a temptation to go for the quick fix, but that can lead to even bigger problems down the track.
Q: The discovery of combustible cladding can be quite a big and expensive job. What is the best way to approach this type of remediation project?
A: Working upfront with the building owner/manager, known in the industry as early client involvement, can make a big difference.
The initial investigations can be quite limited and often doesn’t look at the best way to complete the remediation.
Preliminary investigation can often be confined to whether the aluminium cladding is flammable or not.
Q: What do you think is the preferred approach?
A: Putting together a comprehensive investigation report pays dividends in the long run.
In the case of aluminium cladding, how it is fixed to a building can vary.
You may be working on a building, and the first 14 levels are a cassette system on a frame, and then the next level will change to a doublesided tape system.
Then you have to stop the entire project; you have to do a redesign and explain to the client not only why the project has stopped, but also why there will be cost variations.
That’s the reason we like to do these projects as an early client involvement project.
Q: How does early client involvement work?
A: This involves a four-step process: first an investigation report is undertaken, then project design, next the important step of getting all authority approvals followed by construction commencement.
This streamlines the whole process – we know exactly what we are dealing with and we have left no room for error.
Q: How does early client involvement assist to keep the project within budget and on time?
A: I don’t think there’s many people that understand how the recladding process works and how long it takes and what is involved in it.
It is not as simple as taking a panel off and putting a new one on.
Doing the up-front investigation takes more time, but when compared to delays during the project, there is a significant costbenefit.
Q: How does the approval process work?
A: Under legislation introduced in October 2018, to complete aluminium cladding replacement works you are required to get an authority approval – this can be done by submitting a Development Application, Complying Development Consent or a Fire Order.
Paynter Dixon has a lot of experience in this area. In fact, we were the first company to get approval from the City of Sydney for aluminium cladding replacement work under the new legislation.
View Comments
(0)